Infrastructure
THE QUALITY MANAGEMENT SYSTEM OF THE COMPANY:
The top management of the company has decided the quality policy of the company. Our quality policy is very competent as per CGMP.
QUALITY POLICY :
Arosol chemicals pvt ltd. is in the business of animal feed suppliment since 32 years. Our relentless quest towards quality, commitments, excellence and pride is never ending and our success has continued unabated.
All the products manufactured by us, are of highest quality, safe, effective and the manufacturing operation comply with the International standards. The in- built quality of the product is achieved by Validated technology. Best resources.
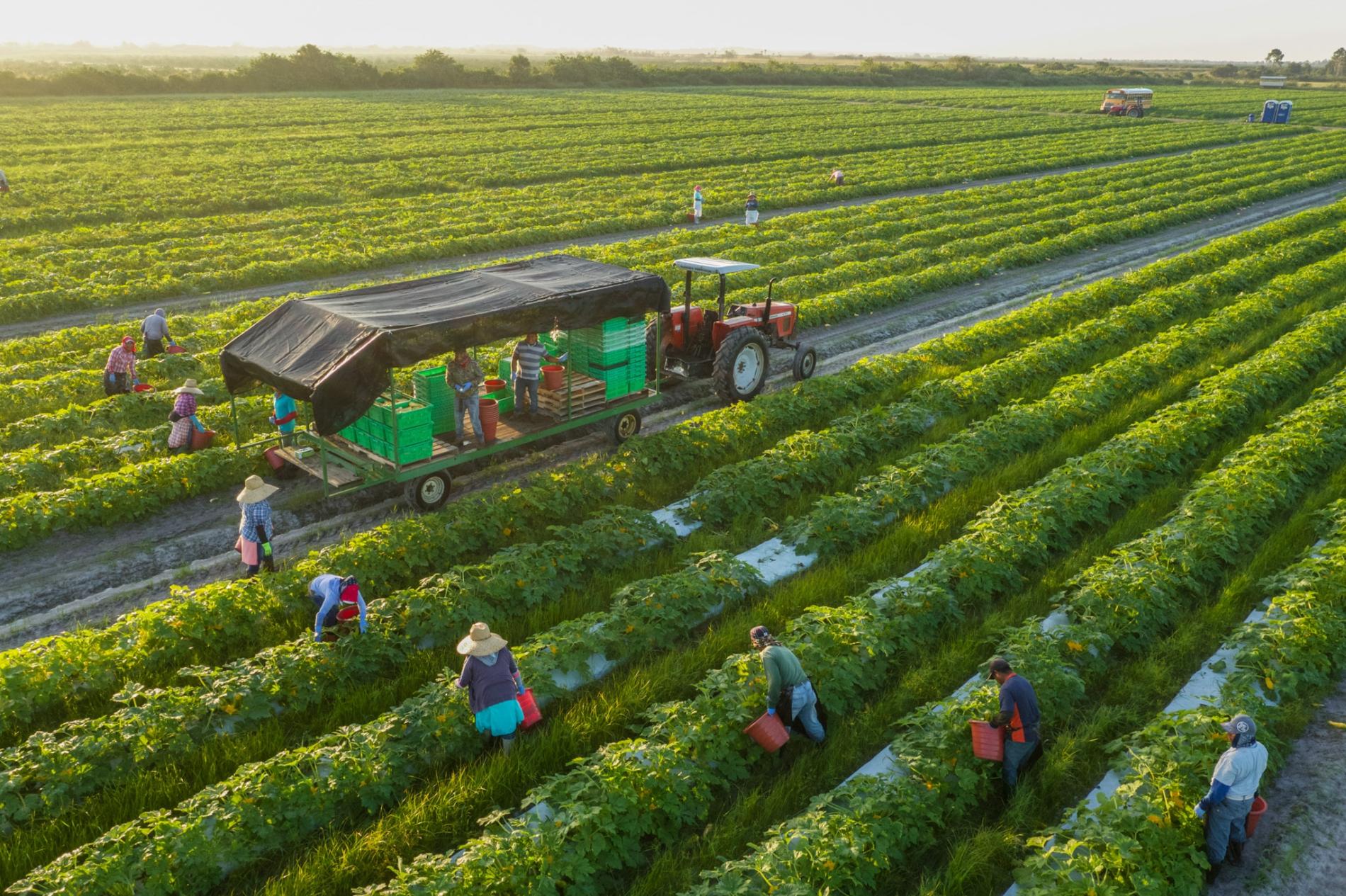
QUALITY MANAGEMENT SYSTEM OF THE FIRM :
Our organization always insists on quality rather than quantity. Towards this, company has instituted the following:
- Developed exhaustive specificationsfrom raw materials, inprocess materials to finished product.
- Validated, approved and documented master formula which form the basis for manufacturing and packing operations.
- Developed adequate in-process controls.
- Descriptive Batch Manufacturing Record (B.M.R.) that mentions even the smallest details related to manufacturing of product.
- Validated, approved and documented analytical procedures.
- The quality assurance department is completely independent of the manufacturing department and reports directly to the plant Manager.
Quality control department is also located at this floor. The laboratory is equipped with sophisticated instruments like H.P.L.C., I.R., U.V. Spectrophotometers etc. Some of the functions of Quality control department are as follows
A. CALIBRATION OF EQUIPMENT:
All the analytical equipments and instruments are calibrated at regular frequencies by an outside agent as per the written procedure and the records are maintained. Instruments log sheets are maintained indicating the usage, calibration and major servicing if any
B. ANALYSIS OF RAW MATERIALS:
Materials are analysed as per the specification and the reports with raw data are checked and preserved. After analysis, A copy of the report is sent to the stores departments.
A representative sample is kept as a control sample and preserved at least 6 months after the expiry date.
A record is maintained for the control samples, which indicates the quantity removed for tests (if any), quantity available etc
STABILITY TESTING:
Stability testing of finished product is carried out as per ICH guidelines and if any change then we adopt following criteria for stability study
- Change in formulation – Accelerated and long-term condition – 3 batches.
- Change in manufacturing process – Accelerated and long-term storage condition – 3 batches.
- CHANGE in source – accelerated and long term storage condition – 3 batches.
- Change in batch size up to 10 times - one batch on long term storage condition.
- Change in location – one batch on Accelerated and long term storage condition.
- Change in primary container – closure system – 3 batches on accelerated and long term storage condition.
- Change in manufacturing equipment (s) having different operating principle – Three batch on long term storage condition.
BASIC, IN-SERVICE TRAINING AND RECORDS:
The company has well qualified persons to carry out entire operations effectively and efficiently. Company has induction programmes for newly recruited employees at all levels. In house training programmes are conducted for all employees at regular intervals to impart required skills in good manufacturing practices.
Company invites regularly external training agencies to conduct training sessions, seminars, symposium and training records are maintained accordingly.
HEALTH REQUIREMENTS FOR PERSONNEL ENGAGED IN PRODUCTION:
At the time of appointment of an employee, they undergo medical checkup by the company’s doctor to ensure he/she is free from any contagious disease or any serious disease. All the employees are subjected to regular medical check up yearly and relevant records are maintained. The employees who work in visual checking section are also subjected for eye test twice a year. Following tests are employed to assess the medical fitness of employees –
- Eye test.
- Blood Pressure test
- Contagious Disease test
- Penicillin Sensitivity test
BRIEF DESCRIPTION OF MAJOR EQUIPMENT USED IN QUALITY CONTROL LABORATORIES :
QUALITY CONTROL DEPARTMENT:
Major instruments used in Quality Control Laboratory are:
S.No | Equipment | ID No. | Calibration period |
1 | UV SPECTROPHOTOMETER | 1 | 1 Year |
2 | IR 8400 (Shimadzu) | 1 | 1 Year |
3 | HPLC (Shimadzu) | 1 | 1 Year |
4 | ELECTRONIC BALANCE 9Dhona 200 D) | 2 | Weekly |
5 | OVEN | 2 | Weekly |
6 | MELETING APPARATUS | 3 | Weekly |
7 | BURSTING STRENGTH TESTER (MULLEN TYPE) | 5 | Monthly |
8 | INCUBATOR | 2 | 6 Monthly |
9 | FALLING SPHERE VISCOMETER | 4 | Monthly |
10 | MICROSCOPE | 2 | 6 Months |
11 | PH METER Microprocessor Based | 3 | Daily |
12 | DISTILLATION APPARATUS ( SS TYPE) | 10 | 6 Months |
13 | TLC APPRATUS MANNUAL | 4 | Monthly |
14 | MINI PUL VURISER | 2 | 6 Months |
15 | MOISTURE METER | 1 | 6 Months |
16 | HOT PLATE | 4 | Monthly |
17 | REFREEGRATOR | 2 | 6 Months |
18 | PHYSICAL BALANCE | 4 | 6 Months |
19 | DIGITAL BALANCE | 3 | Daily |
20 | AUTO CLAVE ( TOSHIBA) | 1 | 6 Months |
2 | MUFFLE FURNACE | 1 | 6 Months |
CONSTRUCTION AND FINISHING:
The walls and floors of entire factory have smooth finish. Entire flooring is made up of Kota Stone with smooth finish to withstand the heavy material / man movement and can be easily washable.
PRODUCT CHANGE OVER:
Swab Tests are carried out when a new product is taken for manufacturing . We take swab on the inlet grills to ensure that it is free from previous product.
AREA FOR THE HANDLING OF HIGHLY TOXIC, HAZARDOUS AND SENSITIZING MATERIAL:
Separate restricted area is provided for storage of Isopropyl alcohol and methylene chloride in raw material store. SOP for storage of I.P.A. and methylene chloride is prepared and displayed.
In quality control department fuming cupboard is provided. The cupboards for flammable solvent are placed away from the flame. Fume cupboards are fitted with a ceramic base and drainage within the hood. Switches and other controls are fitted outside the cupboards
HANDLING OF COMPLAINTS AND PRODUCT RECALLS:
After receiving the complaints from marketing departments, party or through the field personnel, it is forwarded to the Q.C. manager through G.M.(Technical) in prescribed format and the same is recorded in the complaint register.
Q.C. / Q.A. both together investigates the complaints and records the outcomes. It is intimated to the party through the marketing department.
If required, control samples of the same batches are analyzed and the results are compared. Necessary actions are taken, based on the nature of complaint. Remedial measures will be taken to avoid re-occurrence.
If any change in formulation is required, it is initiated by Q.C./Q.A. Manager by written instruction to formulation development department.
In case there is no need to recall the product then a suitable reply along with Investigation report sent to the client. In case product recall is required then the distribution department is instructed to stop the further distribution and issue letter to the Stockist / Distributors to send back the product
QUALITY CONTROL SYSTEM AND PROCEDURE FOR THE RELEASE OF FINISHED PRODUCTS:
Quality control system monitors and maintains the quality of entire operation and the in-process checks at every stage. Specifications, documentation, release procedures, sampling, destruction and analysis are key points.
Q.C. is independent of the production department and reports to the top level Management. The quality control laboratory is responsible for following
- To prepare detailed instruction in writing for carrying out each tests and analysis.
- To analyze each & every consignment of raw materials and packing materials.
- To release or reject bulk-finished products if required.
- To release or reject each batch of finished product that is ready for distribution.
- To evaluate the quality and stability of finished products, and when necessary of Raw Material and bulk finished products.
- To establish shelf life and storage requirements on the basis of stability tests related to storage condition.
- To examine returned goods as to whether such product are released after reprocessing or destroyed.
- To ensure that the manufacturing activities are carried out as per standard operating procedure.
- To carry out random checking of different parameters during different stages of manufacturing/ packing.